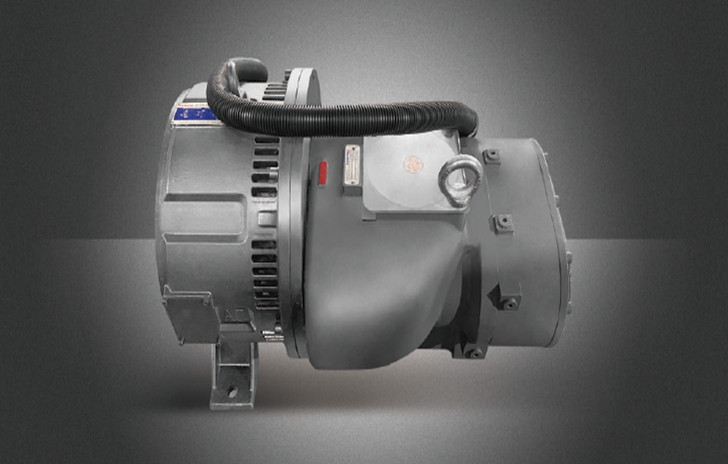
The electric motor is a crucial element in an air compressor, responsible for driving the pistons or rotary components that compress air. Below are the essential principles governing the operation of electric motors in air compressors:
1. Electromagnetic Induction
Electric motors function based on electromagnetic induction. When an electric current flows through a conductor, it generates a magnetic field that causes movement. In air compressors, the motor is powered by either alternating current (AC) or direct current (DC), depending on the motor design.
2. Types of Motors
- Induction Motors (AC Motors): The most commonly used motors in air compressors, relying on electromagnetic induction to create a rotating magnetic field that interacts with the rotor to produce motion.
- Universal Motors (DC Motors): Typically used in smaller compressors, these motors can operate on both AC and DC power, offering simplicity but shorter lifespans due to brush wear.
3. Energy Conversion
The electric motor transforms electrical energy into mechanical energy, powering the piston or rotary mechanism that compresses air. This conversion is crucial for generating the required air pressure and volume.
4. Torque and Rotation
The motor generates torque (rotational force) on its shaft, which is transferred to the compressor’s pump or mechanism, enabling air compression. Torque directly impacts compressor performance, influencing both pressure and airflow.
5. Speed Control
Motor speed significantly affects compressor efficiency. AC motors typically operate at fixed speeds, while DC motors allow for speed adjustments by modifying voltage. More advanced systems incorporate variable-frequency drives (VFDs), which adjust motor speed in response to demand, improving energy efficiency.
6. Cooling
Electric motors generate heat, necessitating cooling mechanisms. Air-cooled motors use airflow to dissipate heat, while water-cooled motors utilize water for temperature regulation, ensuring optimal motor performance and longevity.
7. Power Rating and Efficiency
The motor’s power rating determines the compressor’s capacity, with higher horsepower allowing the compressor to generate more compressed air. Energy efficiency is vital for minimizing operational costs, as a more efficient motor produces greater output per unit of electricity, lowering electricity expenses over time.
8. Start-up Mechanism
To overcome initial resistance during startup, electric motors in air compressors often use start-up capacitors or inrush current limiters. This ensures smooth motor operation without causing electrical issues.
Main Components of an Air Compressor Electric Motor
The electric motor consists of two primary components: the stator and the rotor.
- Stator: The stationary component of the motor connected to the electrical supply, creating a rotating magnetic field when energized.
- Rotor: The rotating part that is influenced by the magnetic field from the stator and generates mechanical movement.
These components interact to generate rotational force (torque), which powers the compressor.
Rotation Speed
The synchronous rotation speed of an induction motor depends on the supply frequency and the number of poles. In practice, the rotor speed is always slightly less than the synchronous speed due to slip (typically 1-5%). Permanent magnet motors experience no slip.
Efficiency
Motor efficiency refers to how effectively electrical energy is converted into mechanical energy. Losses from resistance, ventilation, magnetization, and friction reduce overall efficiency, which impacts operating costs and performance.
Insulation Class
Motor insulation classes determine the maximum temperature the windings can withstand. These classes are denoted by letters (B, F, H) and specify upper temperature limits to prevent insulation degradation and extend motor life.
Class | Max Winding Temp (°C) | Ambient Temp (°C) | Temp Increase (°C) |
B | 130 | 40 | 80 |
F | 155 | 40 | 105 |
H | 180 | 40 | 125 |
Protection Classes
According to IEC 60034-5, protection classes define a motor’s resistance to physical contact and water ingress. These are denoted by IP followed by two digits: the first for protection against solid objects and the second for water protection.
- IP 23: Protection against objects over 12 mm and water spray up to 60° from vertical.
- IP 54: Protection against dust and water sprayed from all directions.
- IP 55: Protection against dust and low-pressure water jets from all directions.
Cooling Methods
Cooling methods, defined by IEC 60034-6, include:
- IC01: Non-ventilated cooling
- IC411: Self-ventilated, internal cooling
- IC00: Forced cooling
These methods are selected based on the motor’s design and operational requirements to maintain safe operating temperatures.
Installation Method
The motor’s installation method, indicated by IM and four digits (according to IEC 60034-7), describes how the motor is mounted and supported. For example:
- IM 1001: Two bearings with a shaft and a stator body with feet.
- IM 3001: Two bearings, a shaft with a free journal end, and a stator body with a large flange and securing holes.
Star and Delta Connections
A three-phase motor can be connected in either star (Y) or delta (Δ) configurations. A star connection is used for higher voltages, reducing current, while a delta connection is used for lower voltages and higher current. These configurations affect motor performance and voltage levels.
Understanding Torque
Torque is the rotational force generated by the motor, and each motor has a maximum torque it can handle. The motor’s ability to rotate depends on this torque, and exceeding the maximum torque will cause failure to rotate. Torque curves illustrate how the motor performs under varying load conditions.
In summary, the electric motor in an air compressor is essential for transforming electrical energy into mechanical energy that powers the compressor. Understanding the principles of electromagnetic induction, torque, speed control, and energy conversion is crucial for enhancing compressor performance and energy efficiency. Factors such as the type of motor, its power rating, and important attributes like efficiency, cooling methods, and protection features are all critical for maintaining a dependable and cost-effective air compressor system.